Aluminum Die Casting 101: A Comprehensive Overview for Engineers and Designers
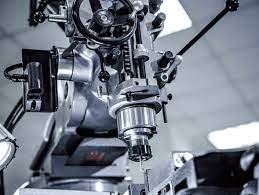
Aluminum die casting is a versatile and widely used manufacturing process that plays a crucial role in the production of a variety of products, ranging from automotive components to consumer electronics. This article aims to provide engineers and designers with a comprehensive overview of aluminum die casting, covering its fundamental principles, advantages, challenges, and applications.
Understanding Aluminum Die Casting
Aluminum die casting is a metal casting process that involves injecting molten aluminum alloy into a steel mold, known as a die, under high pressure. The die is typically composed of two halves, and the molten metal solidifies quickly within the mold, taking the shape of the desired product. Once the casting has solidified, the mold is opened, and the finished product is ejected.
Advantages of Aluminum Die Casting
- High Precision and Complex Geometries: One of the primary advantages of aluminum die casting is its ability to produce aluminum die casting parts and complex shapes with high precision. This makes it an ideal manufacturing method for components with detailed features.
- Cost-Effective Mass Production: Aluminum die casting is well-suited for high-volume production, making it a cost-effective choice for industries that require large quantities of parts. The rapid solidification of the molten metal allows for shorter cycle times, contributing to increased productivity.
- Lightweight and Strong Parts: Aluminum is known for its excellent strength-to-weight ratio. Die-cast aluminum parts are lightweight yet durable, making them desirable for applications where weight reduction is critical, such as in the automotive and aerospace industries.
- Excellent Thermal Conductivity: Aluminum exhibits exceptional thermal conductivity, making it an ideal material for components that require efficient heat dissipation. This property is particularly important in electronic devices and automotive applications.
Challenges in Aluminum Die Casting
While aluminum die casting offers numerous advantages, it is essential to be aware of the challenges associated with the process.
- High Initial Tooling Costs: The creation of the steel molds, or dies, can be expensive. However, the high-volume production capability of aluminum die casting helps amortize these costs over a large number of parts, making it cost-effective in the long run.
- Porosity Concerns: The rapid solidification of molten aluminum can sometimes lead to the formation of porosity in the castings. Proper mold design, process control, and material selection can help minimize porosity issues.
- Limited Alloy Selection: Compared to other casting processes, aluminum die casting has a more limited range of alloys that can be used. However, advancements in alloy development continue to expand the available options.
Applications of Aluminum Die Casting
Aluminum die casting finds widespread applications across various industries:
- Automotive Components: Engine parts, transmission housings, and other critical components in automobiles are often produced using aluminum die casting due to the process’s ability to create lightweight and strong parts.
- Consumer Electronics: The production of lightweight and intricately designed components in devices such as laptops, smartphones, and cameras benefits from aluminum die casting.
- Aerospace Industry: Aluminum die casting is utilized in the aerospace sector for manufacturing components that require a combination of strength and low weight.
- Household Appliances: Many household appliances, including vacuum cleaners, blenders, and coffee makers, incorporate die-cast aluminum parts for their durability and precision.
Conclusion
In conclusion, aluminum die casting is a versatile and widely employed manufacturing process that offers numerous advantages for engineers and designers. Its ability to produce complex shapes with high precision, coupled with the benefits of cost-effective mass production and lightweight yet strong parts, makes it a preferred choice in various industries. Despite the challenges associated with tooling costs and potential porosity, advancements in technology and ongoing research continue to enhance the capabilities of aluminum die casting, expanding its applications and ensuring its continued relevance in modern manufacturing. Engineers and designers can leverage the strengths of aluminum die casting to create innovative and efficient solutions across a diverse range of industries.